機械加工トラブル分析
機械加工トラブル分析
中央労働災害防止協会(中災防)の令和2年度データによると、金属製品製造業での労働災害は3755件、このうち金属加工用機械にかかわる労働災害が884件と最も多く、全体の約24%を占めています。(出典:中央労働災害防止協会 労働災害分析データ)
また労働災害の発生状況として1番多いのは『はさまれ・巻き込まれ』の1237件(約33%)、2番目が『飛来・落下』の459件(約12%)となっており、機械加工で発生しがちなトラブル傾向と一致していることが分かります。
工作機械のNC化率は高く、NCデータミスや設定ミスといったヒューマンエラーによるものが大きな要因であろうと推定できます。
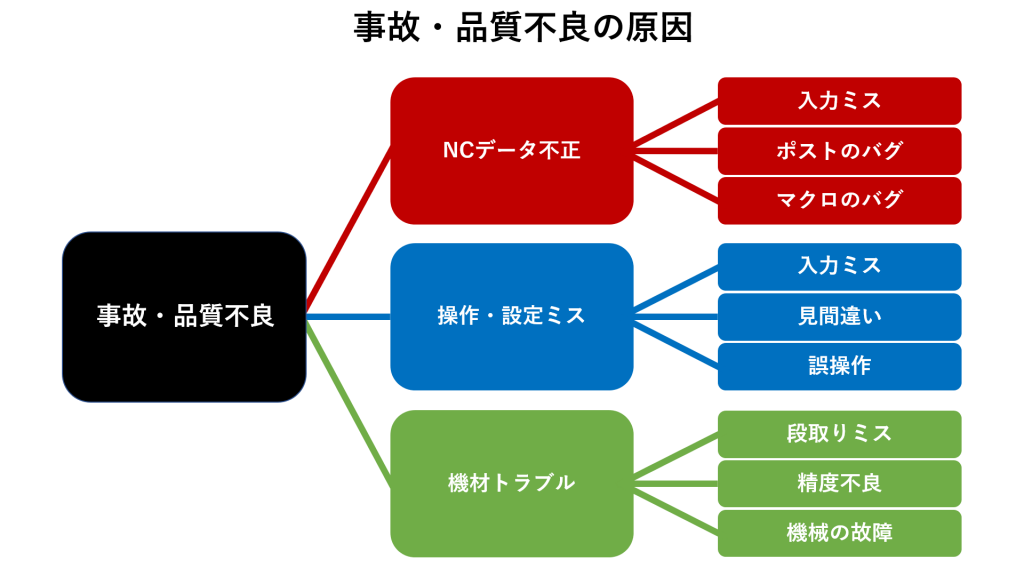
NCVIEWがあれば、NCデータ書式ミス、工具設定ミス、干渉事故といった様々なトラブルを事前検証し、改善することができます。
加工時のトラブル
工具の衝突・破損
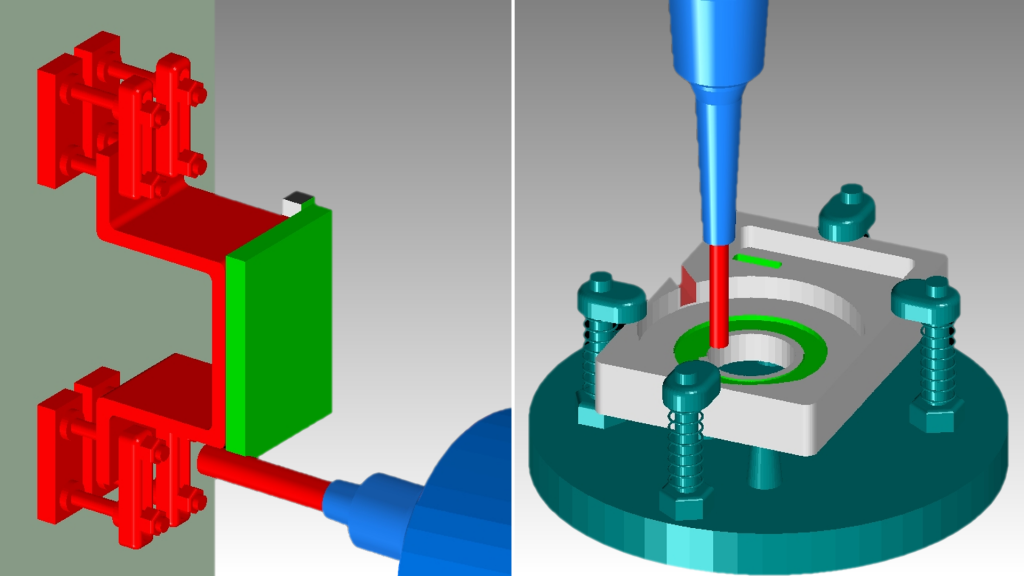
NCデータのミス、またはマニュアル操作でワークや冶具、機械構造物に工具を衝突させてしまうことがあります。
主軸損傷に至ることもある危険な事故です。工具干渉とも言われます。
また被削材の種類、工具の刃数・材質・形状、冷却材、切削速度、回転数、切り屑の排出不良といった様々な要因で、工具が破損するケースもあります。
これらの予測と防止には熟練者の金属加工ノウハウが必要とされますが、NCVIEWの工具・ホルダ干渉チェックがこれを実現します。
内径切削干渉
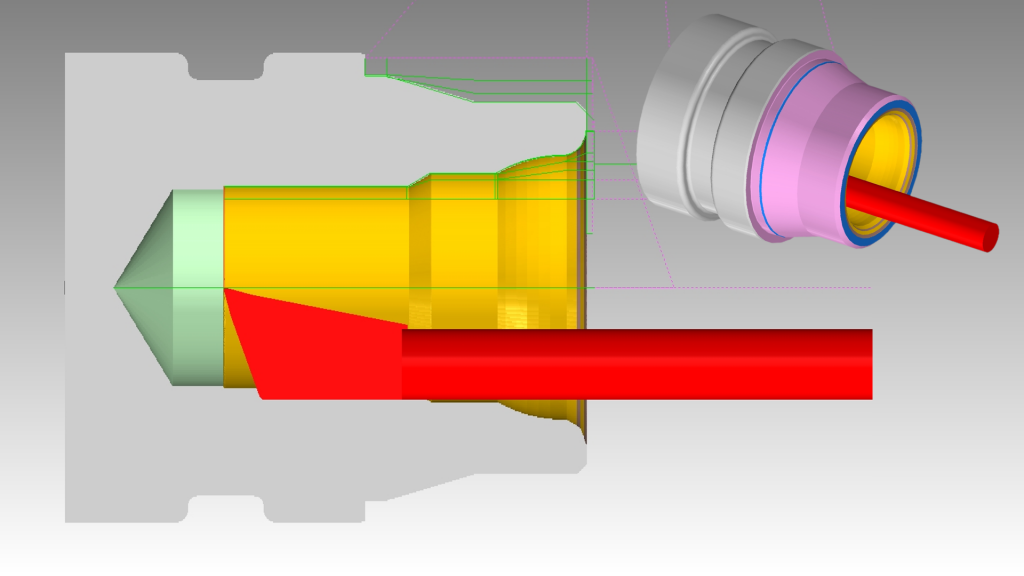
旋盤の内径切削は工具進入の様子を確認しづらく、しばしばホルダ干渉が発生してしまいます。
NCVIEWではこうした干渉も検出してくれます。
干渉回避の方法を探るときにも、旋削のソリッド画面でワーク断面を表示しながら内径加工の工具動作とワークの状態をリアルタイムに観察できます。
主軸損傷
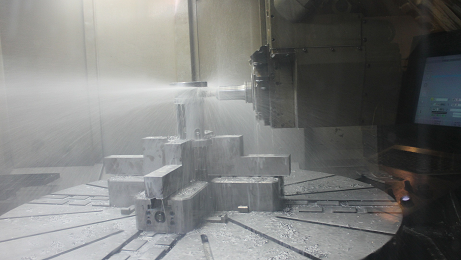
工具やホルダ干渉、構造物干渉が起こってしまうと主軸までも損傷してしまうことがあります。
主軸は加工精度を決定づける重要な機関のため、機械加工の事故の中でも特に避けたいトラブルの一つです。
修理費も高額なうえ、修理期間中は機械が稼動できないため経済的ロスは甚大です。
主軸やテーブルなどの干渉および軸ストロークオーバーチェックにはNCVIEWの機械構造物シミュレーションが役立ちます。
工具折損・タップ・座ぐり漏れ
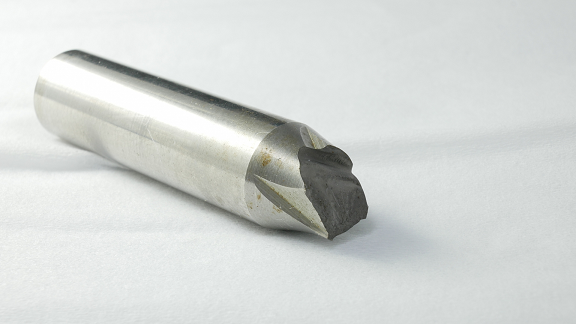
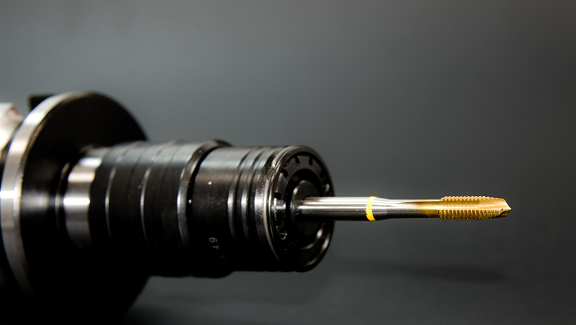
ドリル加工やタップ加工では注意深く作業を進めていても、ワークに折れ込んでしまう加工トラブルがしばしば発生してしまいます。
工具が折れ込んでしまうと、ワークを新たに作り直すか、熟練者に除去を頼むか、放電で溶かすか、などで対処することになります。
納期とコストと品質を考えると、いずれにしても大きなロスになってしまいます。
穴数が多い加工ではタップ漏れ、座ぐり漏れがしばしば起こってしまいます。
特に穴位置が不規則的に配置されている場合は、どれがチェック済みか分からなくなってしまったり、穴を見落としてしまったりなど、目視確認だけでは常に不安が残ります。
作業時間の短縮・品質保証のためには、自動的に穴加工をくまなく検証しレポートしてくれるNCVIEWが役立ちます。
穴加工チェック・穴加工位置検証を使用すれば、下穴およびタップ座ぐり漏れ、穴の深さ不足、穴位置ズレ検証、問題箇所のNCデータブロック特定などによって、穴あけトラブルを防ぐことができます。
切り屑の排出不良
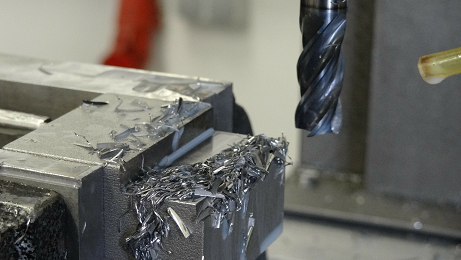
切り屑排出は穴あけ加工の重要な課題ですが、被削材、工具、冷却剤、切削条件などによってその状況は変化してしまいます。
切り屑が詰まると、工具が径方向に振られ加工寸法や工具の寿命などに悪影響が出るほか、製品にもダメージを与える恐れがあります。
穴加工不良
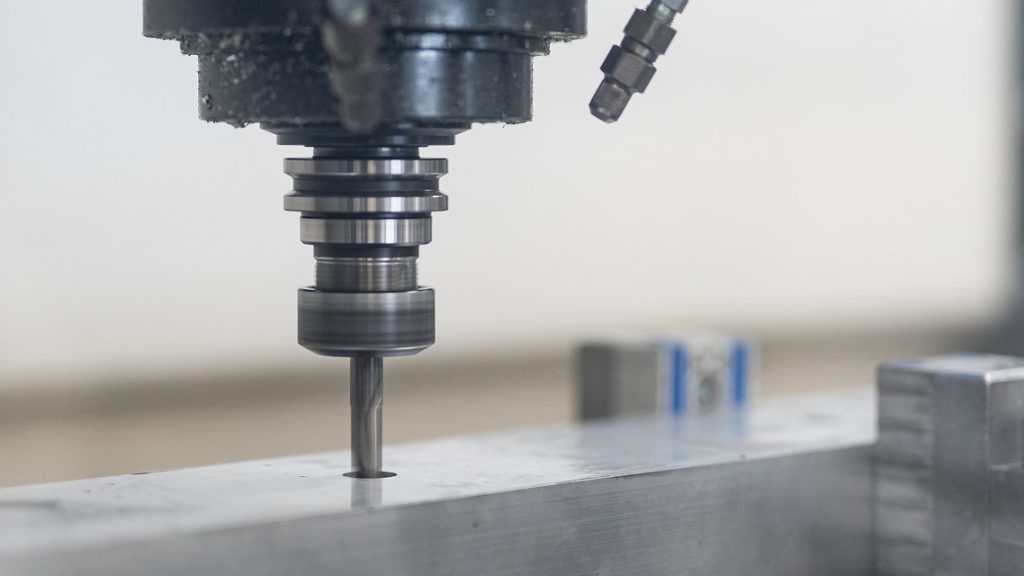
- ドリルの肩高さ・刃の角度・シンニングなどの工具精度
- 工具・被削材・冷却材の性質の相性
- 工具のたわみやビビリ・摩耗・切り屑詰まり・摩擦熱
- 穴の深さ・径・位置決め・下穴の精度
- 送り速度・バックラッシュ
穴加工はこれら様々な要素が複雑に絡み合うため、精度を出すのが難しい加工の一つです。
何らかの原因で穴が偏心したりしてしまうと、その後のリーマ加工やタップ加工、座ぐりにも影響が出てしまいます。
突き出し長不足
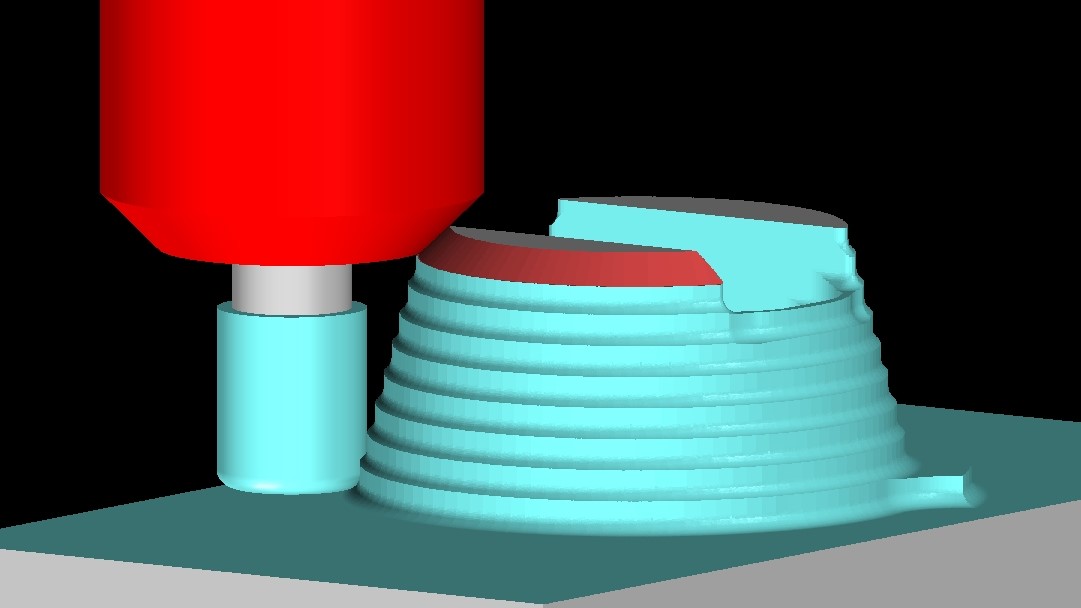
工具のたわみやびびりを抑えて加工を効率化するためには、突き出し長をギリギリまで短く抑えたいところですが、短すぎると今度はホルダや主軸干渉を起こしてしまいます。
NCVIEWの工具長最適化を利用すれば、最短の突き出し長を教えてくれるため、ホルダや主軸干渉を回避することができます。
ヒューマンエラー
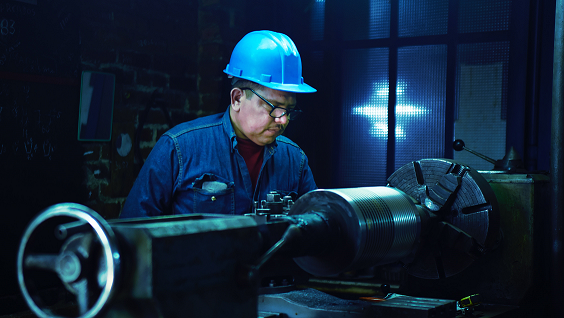
CADでモデリングし、CAMを経由してNCデータを作成したとしても、そのCAD/CAMへ入力したデータに誤りがあった場合、正しいNCデータは得られません。
たとえNCデータが正確でも、NCマクロプログラムにミスがあったり、工具補正量が正しくセットされていなかったり、ワークの位置や向き・座標系の設定が間違っていたりすれば、稼働率低下や品質不良を引き起こし、場合によっては干渉事故にもなり得る重大なトラブルに繋がります。
実機で加工するときと同様の設定環境でシミュレーションを行え、マクロデバッガを持つNCVIEWを利用すれば、加工トラブルを効率的に検証できます。
NCデータのミス
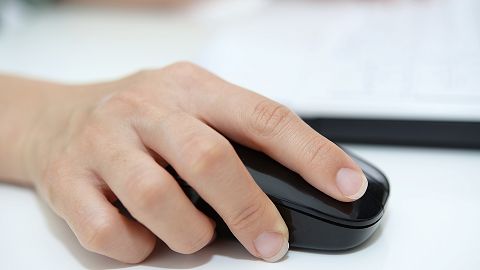
CAM化が進んでいる現在、なぜNCデータのミスが無くならないのでしょうか?
NCデータを作成する方法は多様化しています・・・
- 手入力のNCデータ
- CAM・対話型
- NCマクロ
- CAM・NCマクロ混合
NC工作機械の初期から行われている手入力方式は現在でも多くの工場で行われていますが、対話型やCAMが主要な作成手段となってきているのは間違いありません。
また類似形状加工の多い工場ではNCマクロのテンプレート化やサブプロライブラリー化で効率よく高品質な加工を実現しています。
加工の経験が浅い段階では、CAMでNCデータを作成すればあとは機械が加工してくれると思ってしまいがちですが、被削材一つとっても、硬い/柔らかい、脆い/粘っこい、切り屑の排出が良い/悪い、などの性質がありとても複雑なため、実際の金属加工はそう簡単ではありません。
実際の加工現場では、音を聞いたり振動を感じたりしながら適切な切削条件を探し出していく作業が欠かせません。
その過程でNCデータにも変更を加えているからこそ、NCデータでの最終的な検証作業が必要になります。
これがCAMが出したポスト処理前の中間ファイル(CLデータ)での検証だけでは不十分な理由の一つです。
工具のたわみやびびりを抑える、切り屑を排出させる、バリを出さない、深い穴を精度よく加工する、工具を長持ちさせるなど、熟練技術者にしかできないノウハウはまだ数多く存在します
これらのノウハウが日本の高精度な加工を支えているとも言えますが、一方で熟練技術者は高品質の製品を作れるものの、そうでない作業技術者にはできない、といった技術レベルのバラツキなどの問題も出てしまいます。
このノウハウをCAMに取り込もうという試みは古くからあり、現在ではCAMもかなり進化していますが、熟練技術者の持っている加工ノウハウを最適な形で自動的にNCデータ化してくれるレベルには至っていません。
上述したような金属加工の複雑さがこれを阻んでいます。
最終的なチェックは人間が行う必要があり、それを効率的に行えるシステムがNCVIEWなのです。